Steel plate clamps are indispensable tools in industrial applications where heavy steel plates need to be lifted, moved, or rotated. They are extensively used in industries such as construction, shipbuilding, metal fabrication, and manufacturing. Steel plate clamps not only facilitate the safe handling of heavy materials but also significantly reduce manual labor and the risks associated with lifting and transporting large steel components. Despite their robust design, steel plate clamps are subject to wear over time due to the demanding nature of their applications. This article will explore the use of steel plate clamps, their benefits, and strategies for reducing wear to prolong their lifespan and maintain operational efficiency.
Overview of Steel Plate Clamps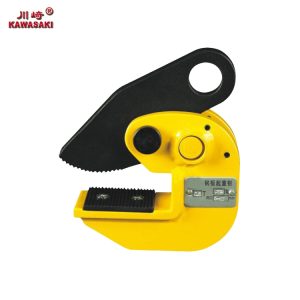
Steel plate clamps are mechanical devices designed to grip and secure steel plates during lifting operations. They typically consist of the following components:
- Body: The main structure that houses the clamping mechanism.
- Cam or Jaw: A gripping element that applies force to hold the steel plate securely.
- Locking Mechanism: Prevents the clamp from opening unintentionally during lifting.
- Swivel Shackle or Hook: Connects the clamp to a crane or hoist, allowing for multidirectional movement.
There are two primary types of steel plate clamps:
- Vertical Plate Clamps: Used for lifting plates in a vertical orientation. They are ideal for applications where plates need to be lifted upright or rotated.
- Horizontal Plate Clamps: Designed to handle plates in a flat, horizontal position, often used in pairs for stability.
Applications of Steel Plate Clamps
Steel plate clamps are used in a variety of industrial settings, including:
- Construction Sites: For lifting steel beams, plates, and other components during building assembly.
- Shipyards: To handle large steel panels used in shipbuilding.
- Metal Fabrication Shops: For moving steel plates between cutting, welding, and finishing stations.
- Warehouses: To load and unload steel plates for storage or transport.
The versatility of steel plate clamps makes them a critical tool for ensuring efficiency and safety in material handling.
Advantages of Steel Plate Clamps
Steel plate clamps offer several benefits:
- Enhanced Safety: By providing a secure grip, clamps reduce the risk of accidents caused by slipping or falling plates.
- Versatility: They are compatible with various plate sizes, weights, and orientations.
- Efficiency: Clamps allow for quick and easy handling of heavy materials, reducing downtime.
- Durability: Constructed from high-strength materials, they are designed to withstand rigorous use.
Despite these advantages, the effectiveness and longevity of steel plate clamps depend on proper use, maintenance, and measures to mitigate wear.
Causes of Wear in Steel Plate Clamps
Steel plate clamps are exposed to numerous forces and conditions that can lead to wear over time. Common causes include:
- Friction: Continuous contact between the clamp’s gripping surfaces and the steel plates leads to gradual abrasion.
- Overloading: Exceeding the clamp’s weight capacity accelerates wear and can cause permanent damage.
- Improper Alignment: Misaligned plates create uneven stress distribution, increasing wear on specific parts.
- Environmental Factors: Exposure to moisture, dirt, and corrosive substances can degrade materials.
- Insufficient Maintenance: Lack of regular inspection and lubrication contributes to wear and reduces performance.
Understanding these factors is crucial for implementing strategies to minimize wear.
Strategies to Reduce Wear in Steel Plate Clamps
To extend the lifespan of steel plate clamps and ensure their continued reliability, it is essential to adopt preventive measures. The following strategies can help reduce wear:
1. Proper Selection of Clamps
- Choose clamps that are suitable for the specific application, considering factors such as plate size, weight, and orientation.
- Use clamps with a higher load capacity than the maximum expected load to reduce stress on the device.
2. Regular Inspection and Maintenance
- Conduct routine inspections to identify signs of wear, such as cracks, deformations, or worn gripping surfaces.
- Lubricate moving parts regularly to minimize friction and ensure smooth operation.
- Replace worn or damaged components promptly to prevent further deterioration.
3. Optimal Usage Practices
- Ensure proper alignment of the steel plate and clamp to distribute stress evenly.
- Avoid abrupt or jerky movements during lifting to reduce dynamic forces on the clamp.
- Do not exceed the manufacturer’s specified load capacity.
4. Use of Protective Coatings
- Apply anti-corrosion coatings to protect clamps from moisture and chemicals.
- Consider surface treatments, such as hardening or plating, to enhance resistance to wear.
5. Training and Supervision
- Train operators on the correct use and handling of steel plate clamps.
- Provide clear instructions on load limits, alignment, and lifting techniques.
6. Environmental Control
- Store clamps in a dry, clean environment to prevent exposure to corrosive agents.
- Use covers or enclosures to shield clamps from debris and environmental contaminants during operations.
7. Use of Auxiliary Equipment
- Employ padding or protective inserts between the clamp and the steel plate to reduce direct contact and minimize abrasion.
- Consider using lifting beams or spreader bars to distribute loads evenly.
Case Studies: Reducing Wear in Industrial Applications
Shipbuilding Industry
In a large shipyard, frequent lifting of heavy steel panels resulted in rapid wear of steel plate clamps. By implementing a maintenance schedule that included weekly inspections and lubrication, the company reduced clamp failures by 40%. Additionally, operators were trained to align clamps correctly, minimizing uneven stress and further extending clamp lifespan.
Metal Fabrication Shop
A fabrication shop handling thin steel plates faced issues with grip slippage and jaw wear. The shop introduced protective rubber pads on the jaws to reduce direct contact with plates, significantly decreasing wear without compromising grip strength. This small investment saved thousands in replacement costs over a year.
Conclusion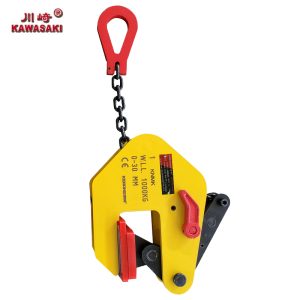
Steel plate clamps are vital tools for safe and efficient material handling in heavy industries. However, the demanding nature of their applications subjects them to wear over time. By understanding the causes of wear and implementing strategies such as proper selection, maintenance, and usage practices, it is possible to enhance the durability and performance of these essential devices. With the right approach, businesses can reduce downtime, lower operational costs, and maintain a safe working environment, ensuring that steel plate clamps remain reliable for years to come.